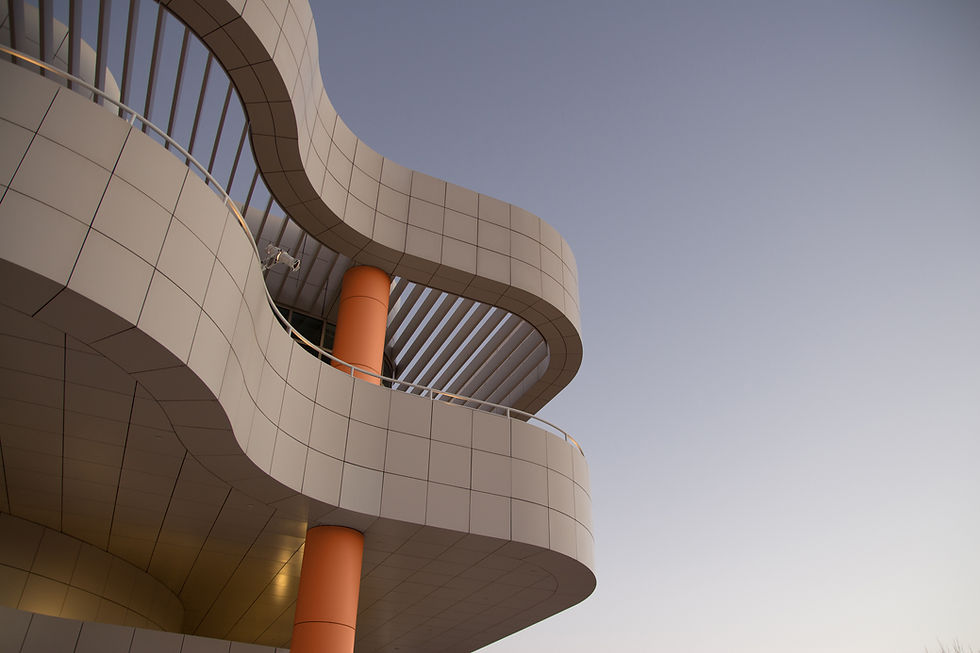
Ensure Perfect Alignment with a Straight Edge Tool [2024]
Aug 26, 2024
4 min read
0
0
0

Aligning surfaces, materials, or components with precision is critical in various fields, from woodworking to metalworking, machine calibration, and beyond. Achieving such alignment often necessitates the use of a straight edge tool—a simple yet indispensable device that ensures surfaces are flat and linear to an exacting degree. This article explores how to ensure perfect alignment with a straight edge tool, covering everything from the tool’s types and applications to maintenance and troubleshooting.
Introduction to Straight Edge Tools
A straight edge tool is a flat, straight piece of material used to check the straightness of surfaces. These tools are essential in any application where alignment and precision are necessary, providing a reliable reference to verify that a surface is level and true. Historically, straight edge tools have evolved from rudimentary wooden devices to highly engineered steel or granite instruments used in industrial applications today. The need for precise measurements and alignment has driven innovations in these tools, making them indispensable for professionals across various industries.
Types of Straight Edge Tools
Straight edge tools come in different materials, each suited for specific applications.
Steel Straight Edges: Known for their durability and weight, making them ideal for heavy-duty industrial tasks.
Aluminum Straight Edges: Lighter than steel, suitable for tasks requiring easy handling without compromising accuracy.
Granite Straight Edges: Extremely precise, used where a high degree of flatness is essential.
Hybrid Material Straight Edges: Combine different materials to offer a balance between weight, durability, and precision.
Choosing the right type depends on the specific needs of your project.
Applications of Straight Edge Tools
Straight edge tools are versatile, with applications spanning multiple industries:
Woodworking: Ensuring boards are straight, aligning cuts, and checking for warping.
Metalworking: Aligning metal sheets, checking flatness in welding, and ensuring components fit together perfectly.
Machine Tool Calibration: Essential for verifying that machine components are aligned correctly.
Surface Plate Checking: Used to ensure the flatness of surface plates in laboratories and workshops.
Understanding Precision in Alignment
Precision in alignment is about achieving exactness within a specified tolerance level. A straight edge tool helps maintain these tight tolerances by providing a reliable reference point. In many precision tasks, even a slight deviation can lead to significant errors, making the role of straight edges vital in maintaining accuracy.
Key Features of a Quality Straight Edge
When selecting a straight edge tool, consider these key features:
Material Composition: Affects the tool’s durability and application suitability.
Length and Size Options: Longer edges provide better accuracy but are more challenging to handle.
Edge Finishing and Straightness: Critical for high-precision work.
Measurement Markings and Calibration: Some straight edges include markings for quick measurements.
How to Use a Straight Edge Tool for Alignment
Using a straight edge tool correctly ensures optimal results:
Preparation: Ensure the surface is clean and free of debris.
Positioning: Place the straight edge along the surface or material.
Observation: Check for gaps or deviations along the edge.
Adjustment: If misalignment is found, adjust the material or surface until it is perfectly straight.
Ensuring Accurate Alignment in Woodworking
In woodworking, a straight edge is vital for:
Cutting Accuracy: Aligning cuts ensures the edges are true.
Board and Panel Alignment: Ensures pieces fit together without gaps.
Warping and Twisting Checks: Identifies imperfections that could affect the final product.
Ensuring Accurate Alignment in Metalworking
For metalworking, straight edges help with:
Aligning Sheets and Components: Ensures parts are flat and straight.
Welding Precision: Verifies that edges are flush before welding.
Bending and Warping Detection: Helps identify deformations early.
Calibration and Maintenance of Straight Edges
To keep your straight edge tool in top condition:
Calibration: Regularly check the tool against a known reference standard.
Cleaning: Keep it clean and free from corrosion or damage.
Storage: Store properly to avoid warping or bending.
Common Mistakes to Avoid
Common mistakes include:
Misusing the Tool: Using a straight edge on inappropriate surfaces.
Overlooking Surface Preparation: Always clean surfaces before use.
Ignoring Temperature Effects: Temperature changes can affect metal straight edges, leading to inaccurate readings.
Comparing Straight Edges with Other Tools
Straight edges are often compared with other alignment tools like spirit levels and laser levels. While these tools have their place, straight edges offer unmatched precision for specific tasks, particularly when checking flatness over longer distances.
Selecting the Right Straight Edge Tool
When selecting a straight edge, consider:
Application Needs: Different tasks require different types of straight edges.
Budget vs. Professional Options: Invest in a high-quality tool if precision is critical.
Brand Reputation: Choose reputable brands for reliability.
Troubleshooting Alignment Issues
Common alignment issues include:
Warping: Can occur in both the material and the straight edge itself.
Surface Irregularities: Sometimes the problem lies in the surface, not the tool.
Tool Wear: Over time, even the best tools wear out and may need replacing.
Innovative Uses of Straight Edge Tools
Straight edges are not limited to industrial applications. They are also used in:
Artistic Applications: For precise layout work in large-scale art or installations.
Home Improvement: Useful for tasks like checking the flatness of floors or walls.
Gardening: Ensuring straight planting rows.
Frequently Asked Questions About Straight Edge Tool
Q. What is the Best Material for a Straight Edge Tool?
A. Granite is often preferred for high-precision tasks, while steel offers durability.
Q. How Can I Test My Straight Edge for Accuracy?
A. Use a certified reference surface or check it against another straight edge.
Q. What Are the Differences Between Flatness and Straightness?
A. Flatness refers to a surface being even, while straightness relates to a line or edge being true.
Q. Can I Use a Straight Edge Tool for Curved Surfaces?
A. No, straight edges are specifically designed for flat surfaces.
Q, How Often Should I Calibrate My Straight Edge?
A. Depending on usage, calibration should be checked every 6-12 months.
Q. Why Is My Straight Edge Giving Inconsistent Results?
A. This could be due to wear, surface contamination, or temperature variations affecting the tool.
Conclusion
Using a straight edge tool ensures perfect alignment, whether in woodworking, metalworking, or precision tasks. By selecting the right tool, maintaining it properly, and following correct techniques, you can achieve consistently accurate results. Avoid common mistakes, and your straight edge will remain a reliable asset. Precision starts with the right tools—choose wisely and maintain regularly.